If you google “how to model an avalanche”, you’re likely to turn up almost entirely results about computer modeling of avalanches. Not helpful! I went into this one mostly on my own.
In the end I’ll have 2 avalanche paths on the KD – The McRae canyon/Paulson Gap slops with snowshed, and one at mile 93.6 of the Nelson sub along Kootenay Lake with a slide fence and perhaps signals. The latter is a long way off, but I’ve finished (I think) the former.
The shed is partially scratchbuilt, with stripwood sheathing and roof over laser cut bents, as cut by RS Laser. The background is by my partner Adrienne. The snowshed sits on a base carved from thick plaster of paris, shaped as it set to be the correct profile.
I’m modeling mid spring, so there’s still the remainders of avalanches on the slope and shed, mostly where they came to rest, at their thickest, but the slope itself shows signs of being recently covered – still brown since spring was delayed waiting for melt. This means a whole lot of brown tones.
You can do whatever you want to get the desired base shape. I prefer to use plaster, and once I had that to my liking, I started off with a layer of dirt tone paint (varies by location) with varied random-ish splashes of both real dirt from the area and earth blend ground cover. (Either scenic express or woodland scenics are good.) After these were dry, I sprayed a good layer of 1:3 white glue:water over the whole area and sprinkled some random rocks and dead static grass (by hand, no applicator) and did a little finger finessing to get it pointed down the slope if it looked wrong. The top layer were the bushes that are present on most avalanche paths – protected and weighed down by snow, they’re not demolished by slides the way trees are. I used Scenic Express Supertrees that I spray painted brown. On the sides of the slope, I sprayed a little extra glue on them and sprinkled a bit of fine green ground foam on to simulate fresh buds. Either side of that, there’s an abrupt line of mature trees that haven’t been touched by sliding snow. At the bottom is bare rock, but that’s specific to my location with its shed – you will want scattered rocks brought down by the avalanche around, but not necessarily exclusively. Definitely lots of dead trees – whether the packaged ones by Woodland Scenics or the ones I made from both Supertree trunks or bamboo skewers.
Now the piece de resistance! Leftover snow. Way easier than it looks. Grab some sculptamold (probably specifically due to its light yet clumpy consistency, can’t think of any substitutions) then press some rocks into it and shape it vaguely to where you want, then spray it with water. When it’s fully wetted you can tease it a little bit into more the shape you want, but you don’t want to do too much and make it lose its lumpy texture. After it’s dry you can wash a tiny bit of brown paint (raw umber-ish) onto small spots to give it that dirty texture, but VERY SPARINGLY.

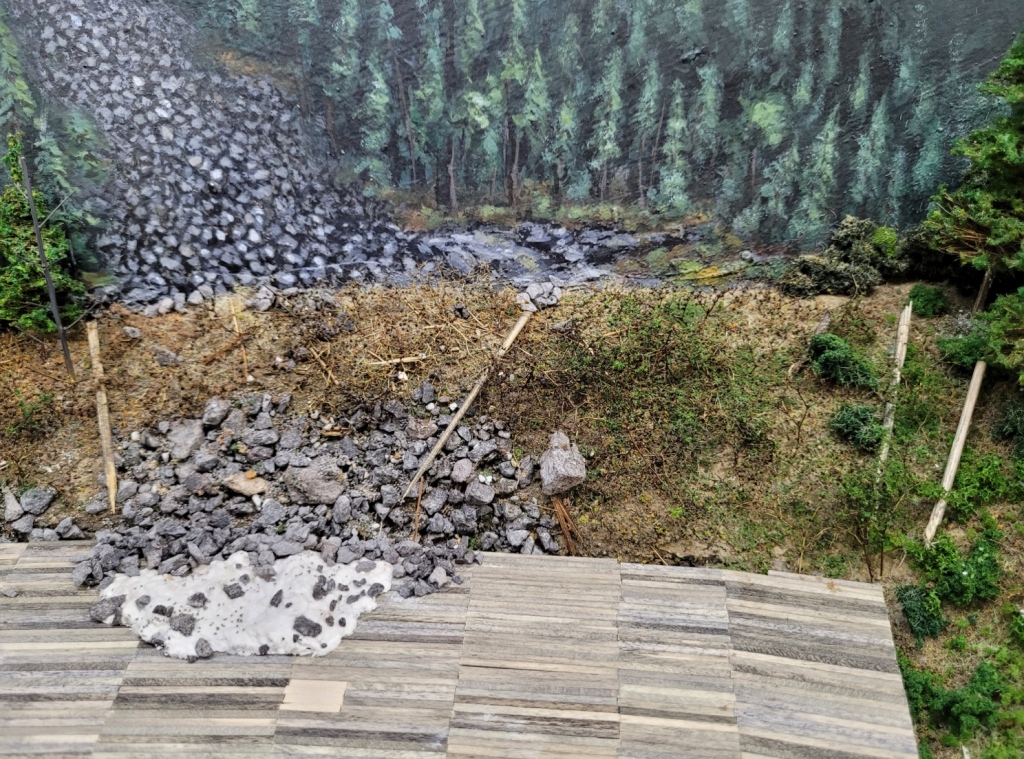
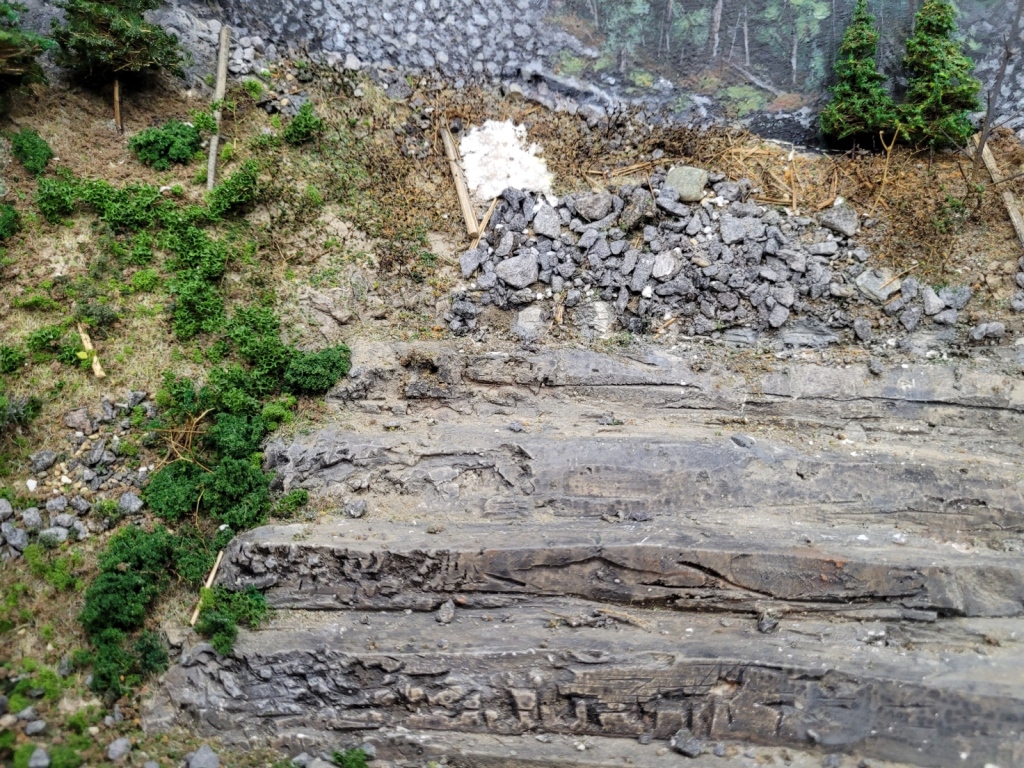
And voila!
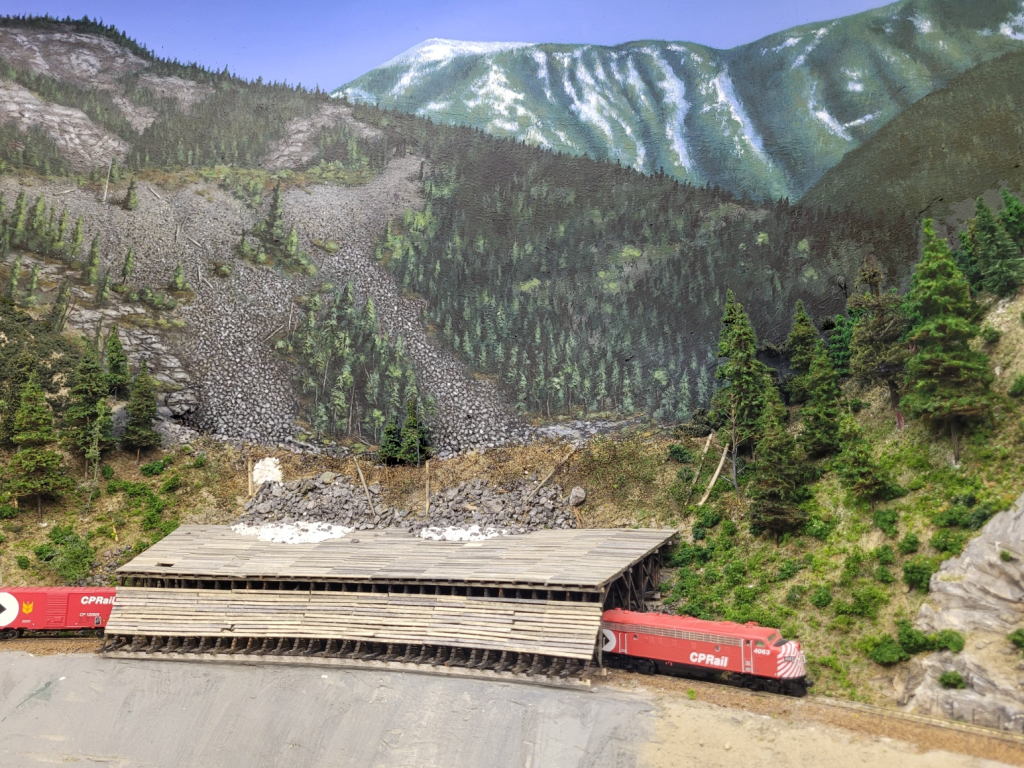